Filtration for the surface treatment for industry
Robust filtration solutions for surface treatment industries to optimize their processes and avoid health and safety risks and reduce environmental impact.
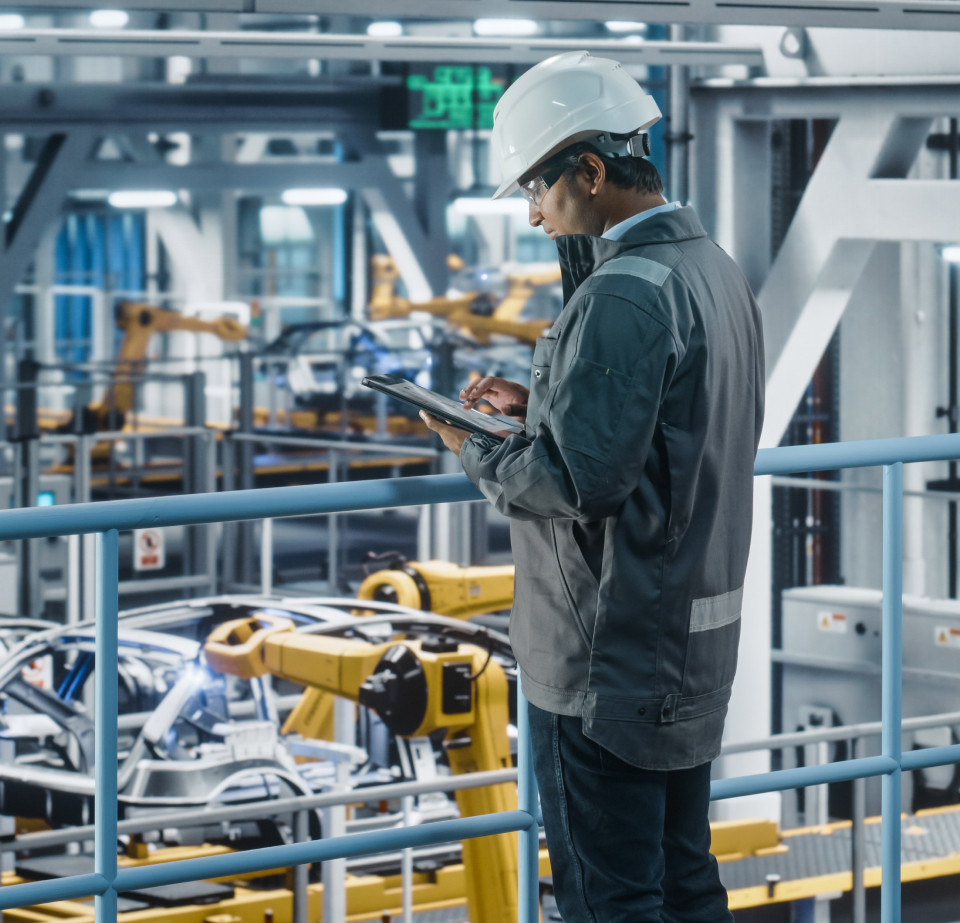
Improve productivity with good filtration
Managing surface treatment, especially in paint lines, presents great challenges. Air quality is of vital importance for proper operation because even the smallest elements can have serious consequences. Contaminated air causes rework, which leads to lower productivity and in extreme cases to line shutdowns.
Air filters are indispensable in the processing of industrial materials. In this sector, high levels of dust and other molecular contaminants are generated, resulting in odours, corrosive reactions that can even pose a toxic hazard to employees and the environment.
They therefore require a controlled environment governed by regulations and requirements to ensure process efficiency and avoid health, safety and environmental risks.
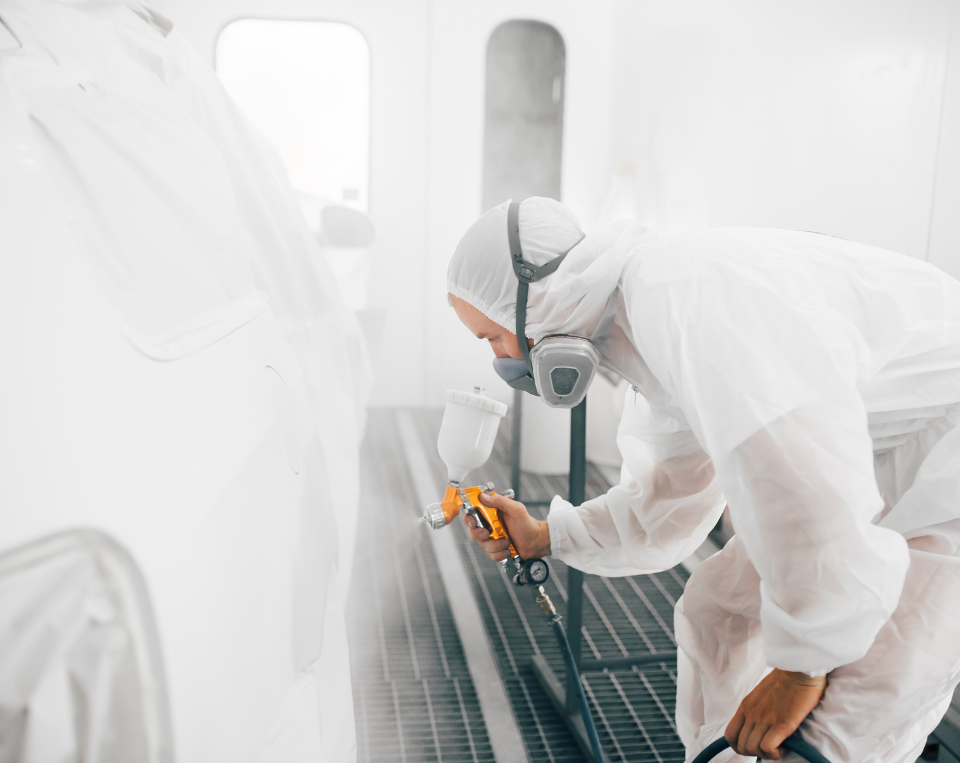
Applications
Click on each application in our Venfilter Safety Spaces range and find out how we can help you improve your processes.
Why air filtration systems for the processing of materials for industry?
Installations for the processing of industrial materials require special air filtration and ventilation systems. Without proper control and treatment, this can become a risk to process efficiency.
The microscopic dimension of the sources of contamination, due to their size, makes the problem more difficult, because the air contains different micro-organisms and particles specific to the activity.
The presence of contaminants in the air during the painting process can negatively affect the efficiency of the process. Airborne particles can clog paint equipment nozzles, causing interruptions and delays in production. Air filtration systems minimise the presence of these particles and keep the work flow smooth and efficient.
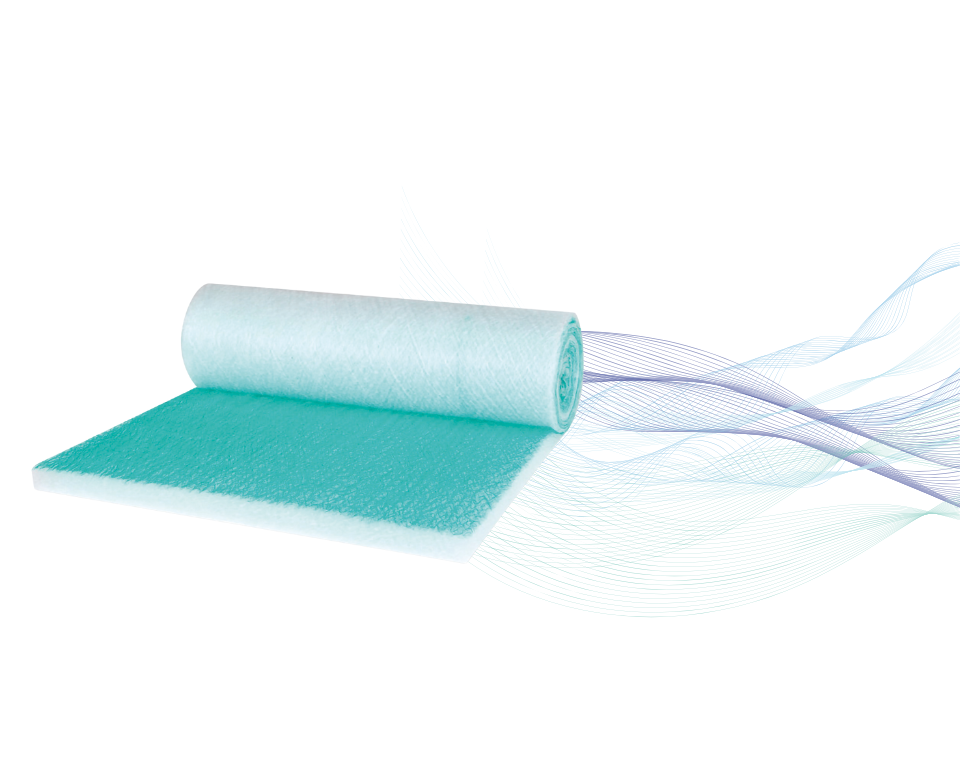
Sources of pollution
CHEMICAL EMISSIONS
The use of paints, coatings and solvents in the surface treatment industry can generate chemical emissions. These volatile organic compounds (VOCs) can be released into the air during paint application and during the drying and curing processes.
PARTICULATES AND DUST
During sanding, polishing and surface preparation processes, particles and dust containing substances such as metals, old paints, oxides and other contaminants can be generated. These particles can cause air quality problems, especially if they contain toxic components such as lead or asbestos.
EMISSIONS FROM EQUIPMENT AND MACHINERY
Industrial surface treatment activities may require the use of equipment and machinery, such as air compressors, heat generators, etc. This equipment can emit exhaust gases, fumes and other air pollutants if not properly used or maintained.
WASTE AND EFFLUENTS
Inadequate management of waste and effluents generated in surface treatment processes can be a source of pollution. Waste paint, solvents and other chemical products must be properly managed to prevent their release into the environment.
CLEANING AND DEGREASING PRODUCTS
The processes of cleaning and degreasing surfaces prior to paint application can also generate pollutants. Solvents used in these processes can emit VOCs and other chemical compounds into the air.
Filter and air conditioning for the processing of materials for industry
Venfilter filters and filter media are certified and comply with the most stringent regulations to meet the needs of the industry.
The air conditioning systems of the installations of these industries must comply with the strictest requirements in terms of protection and safety. They must guarantee the absence of particulate contaminants, especially in the most critical areas. Only systems with efficient filters can provide such controls.
In short, air filtration systems are essential to ensure the quality of paint finishes, protect the health of workers, comply with regulations and standards, improve the efficiency of the painting process and reduce waste and rework in the industry.
Venfilter offers specialised air filtration solutions that provide excellent long-term performance in demanding conditions. Talk to our experts.
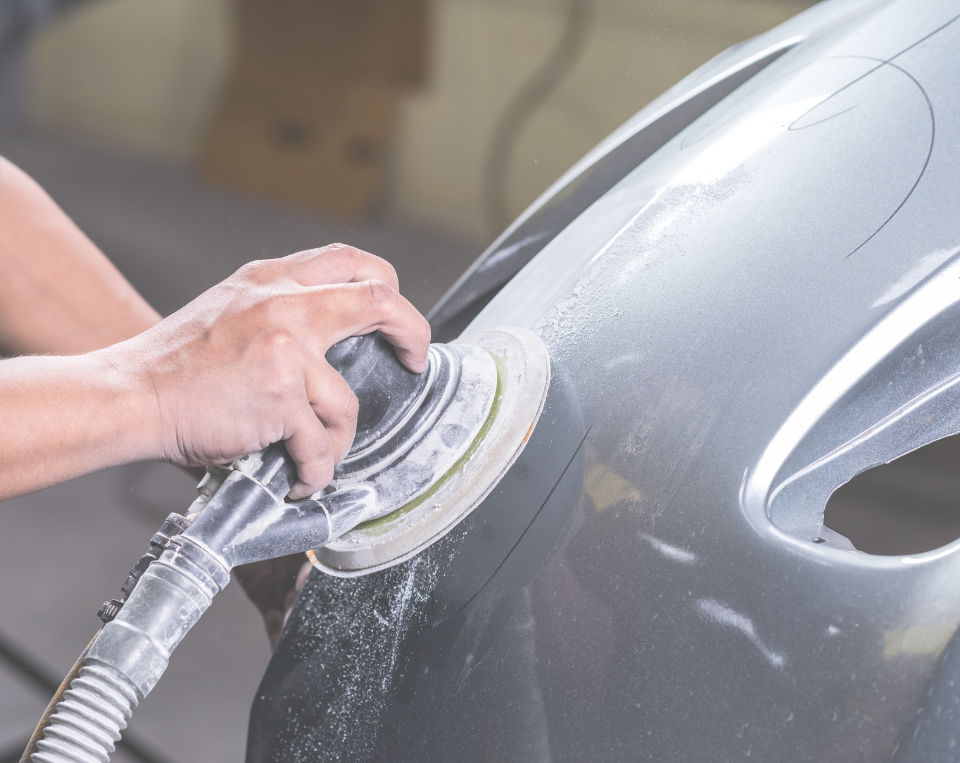